激光熔覆成形的概述: 激光熔覆成形(LCF)是一种能够制造全致密金属零件的3D打印工艺,典型成形工艺有激光近净成形、直接金属沉积(DMD)等,相对于SLM、电子束熔融成形(EBM)等工艺,激光熔覆成形可以制造出更复杂、更大的零件。 激光熔覆成形技术是在计算机控制下,根据零件的三维数据模型,利用高能激光束将粉末材料通过“离散+堆积"的制造方法实现零件的成形与制造。由于其独特的成形方式,能够解决传统加工中难以解决的问题,同时还能实现各种复杂结构零件的快速、无模具、高性能、全致密近净成形,因此被广泛应用于各领域,是一项有着广泛应用前景的高新技术。
成形组织性能: 从宏观上来看,激光熔覆成形制件的尺寸精度和形状精度还达不到理想要求,往往存在着气孔和表面不平整情况;从微观上来看,制件微观组织性能难以控制,易产生裂纹及脆性断裂。这些问题关系着激光熔覆成形制件能否达到所需性能要求,究其原因在于: ①熔覆成形过程涉及的因素很多,包括加工工艺因素、金属粉末特性、环境因素等,这些因素在熔覆成形的极端工艺条件下表现较为复杂,且存在着多参数的相互耦合,因此对其理论建模十分困难; ②熔覆成形过程涉及金属粉末快速熔化和凝固过程,熔池内部高温和熔融金属液的剧烈流动使得熔覆组织性能很难控制。决定金属零件成形质量的关键因素就是单道熔覆层的高度、宽度以及表面成形质量。单道熔覆层质量的好坏直接决定着整个熔覆件的质量和成形效率。研究激光熔覆工艺参数对单道熔覆层高度、宽度以及制件表面质量的影响对最终控制成形质量有决定性的意义。随着扫描速度的增大,熔覆层表面的亮度变得越来越低,表面粗糙程度增大。这是因为扫描速度快、能量吸收不足,部分未熔化的粉末在表面形成了半熔化的黏结堆积点。
在其他条件确定不变的情况下,熔覆层的高度、宽度均随扫描速度的增加而降低。扫描速度的增加,使得单位时间内落人熔池的粉末量相对减少。同时,激光束与粉末接触时间变短,粉末没有充足的时间来吸收必要的能量。随着激光功率的不断增加,单道熔覆层的高度、宽度整体随之增大,增加幅度较为明显。因为功率较低时,基体与熔覆材料均不能得到充足的能量,熔池面积不足,导致单道熔覆层宽度和高度均较低。在这种情况下,少部分未熔化的粉末残留在表面,以致单道熔覆层表面不太光滑。随着送粉速率的增大,单道熔覆层的高度逐渐增大,且增加趋势较平稳。在一定范围内单道熔覆层宽度也平稳增加,随后减小。随着离焦量的增大,单道熔覆层高度越来越小,而宽度则先增大后减小,且变化不太明显。这是因为:在正离焦情况下,随着离焦量增大,光斑逐渐变小,成形宽度也就自然随之减小。但是光斑直径变小,光束的能量密度便增大,就会使成形时单位时间内熔融金属液体积有所增加,因而表现为高度增加。当离焦量进人负离焦区域时光斑直径将会随离焦量的增大而变大,激光束能量密度开始降低。虽然光斑开始变大,进人熔池的粉末量增加,但是由于能量密度降低,部分粉末不能完全熔化,从而减少了单位时间内成形的体积,因此单道熔覆层高度和宽度此时略有下降。
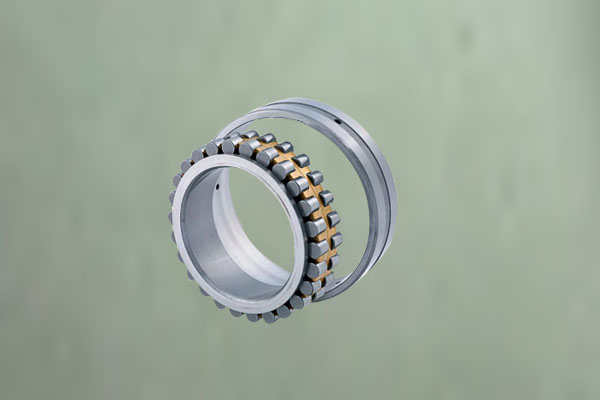
激光熔覆成形过程中熔覆层的显微组织形貌及其性能随着工艺参数的变化而发生变化,工艺参数选择不当,会产生裂纹、气孔、脆性断裂等缺陷,影响成形件的宏观力学性能,因此研究工艺参数对成形组织与性能的影响十分重要。 在我国对金属3D打印激光熔覆成形技术的研究非常多,通过对金属合金的调节和对及其功能的转变,优化工艺参数,可以获得良好的成形制件。未来也会在各个领域得到广泛的发展。3D打印不仅可以提升我国的综合实力,还能让减轻人力、物力、财力。减少材料的浪费,让资源可持续发展。
|