EC-Atech 是一家总部位于香港的原始设备制造商,专门生产墨盒。在产品制作的过程中,“高精度”这一点对该公司至关重要,因为它需要确保最终产品不会发生漏墨、以及没有任何其他印刷缺陷。因此,EC-Atech 致力于开发高标准高质量的产品原型,尤其是在墨盒的固定装置方面。这些固定装置有助于确保墨盒的有效运行,及其在多项打印任务之间保持准确、可重复、和一致的打印方式。为此,固定装置必须做到坚固耐用,且需要根据不同款式墨盒进行定制。
像“高精度”这样的严格标准可能会导致在产品制作过程中无法很好地对产品质量和成本进行平衡。EC-Atech 在与第三方制造商合作进行产品原型开发时就遇到了这样的情况。在根据不同款式墨盒进行固定装置定制的过程中,为了达到严格的标准,团队经常不得不与客户和原型制造商来回沟通。在设计最终完成之前,通常需要进行高达五轮的修订。除了需要多次修订之外,使用金属材质来制作产品原型(该行业的默认方法)还会降低整个制作过程的效率,因为金属生产的交货时间可能在三周到四个月之间。 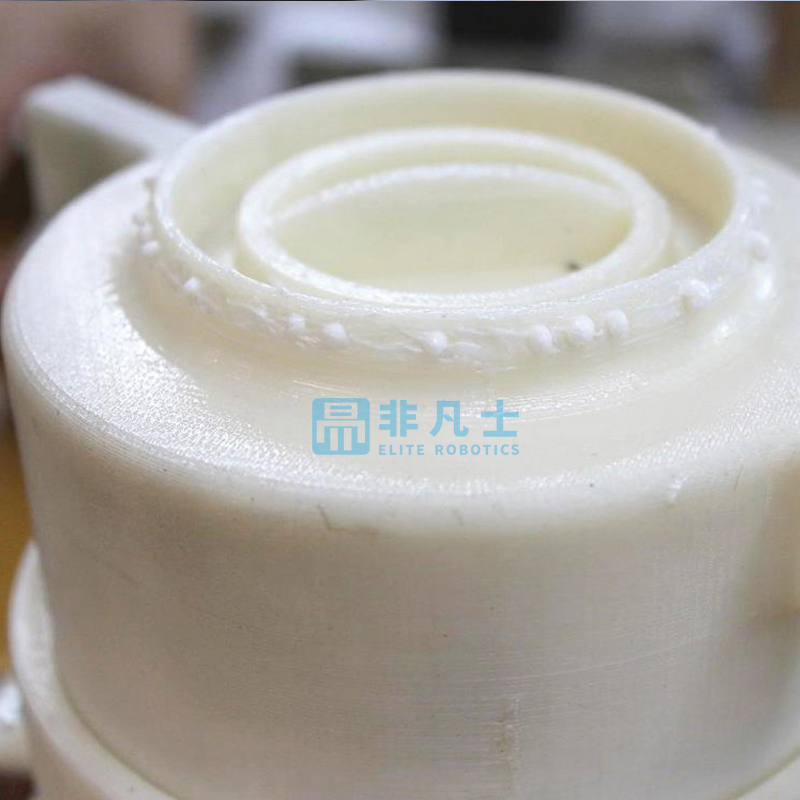
而且,如果需要进行多次设计修订,则原型开发可能需要一年甚至更长的时间。由于这些低效率状况的出现,EC-Atech 觉得有必要简化其整个工作流程。为了生产坚固耐用的定制化产品原型,该公司决定采用FDM 3D打印机,这是一种增材制造技术,可使用生产级热塑性塑料来逐层构建工件。该技术经过优化,可用于制作形状复杂的工件,因此非常适合 EC-Atech。如今,FDM 技术已经成功地帮助 EC-Atech 为 每 款 墨 盒 定 制 固 定 装 置 。 自从将 3D 打印引入其装配线以来,EC-Atech 的产品质量和成本效益都得到了显著改善。由于现在的工具采用了热塑性塑料来代替金属,因此其重量从 20 公斤减少到仅 1 公斤。尽管重量更轻,但质量却丝毫没有降低——因为与金属相比,热塑性塑料在提供强度和稳定性的同时,还具有更强的抗化学侵蚀性 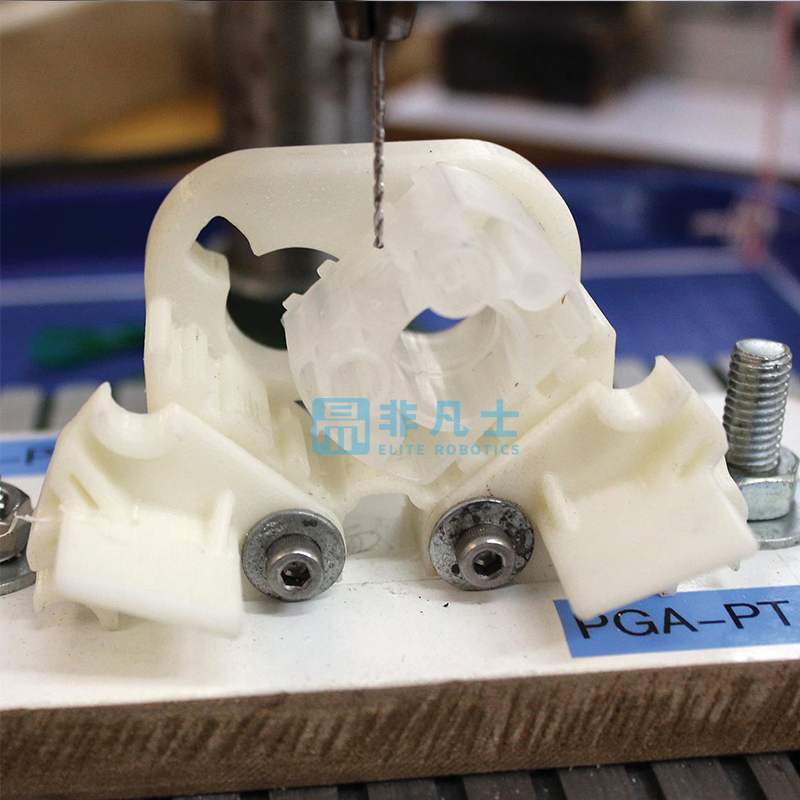
鉴于这种材料的低熔点,生产过程需要降低功率消耗和热量产生,而这同样有助于 EC-Atech 降低能源成本。此外,EC-Atech 现在可以在几周内(而不是几个月内)开发出产品原型。以较短的交货时间和较低的单位成本,即使生产数量少于 100 件,该团队也可以从中获得良好的成本效益。EC-Atech 的副产品经理 Ng Wai Kwong 说:“通过 3D 打印,我们将交货时间从一年缩短到四个月。”“而且,在曾经交货时间的三分之一时间内,我们定制出了重量更轻、成本更低、且非常坚固耐用的组件。” 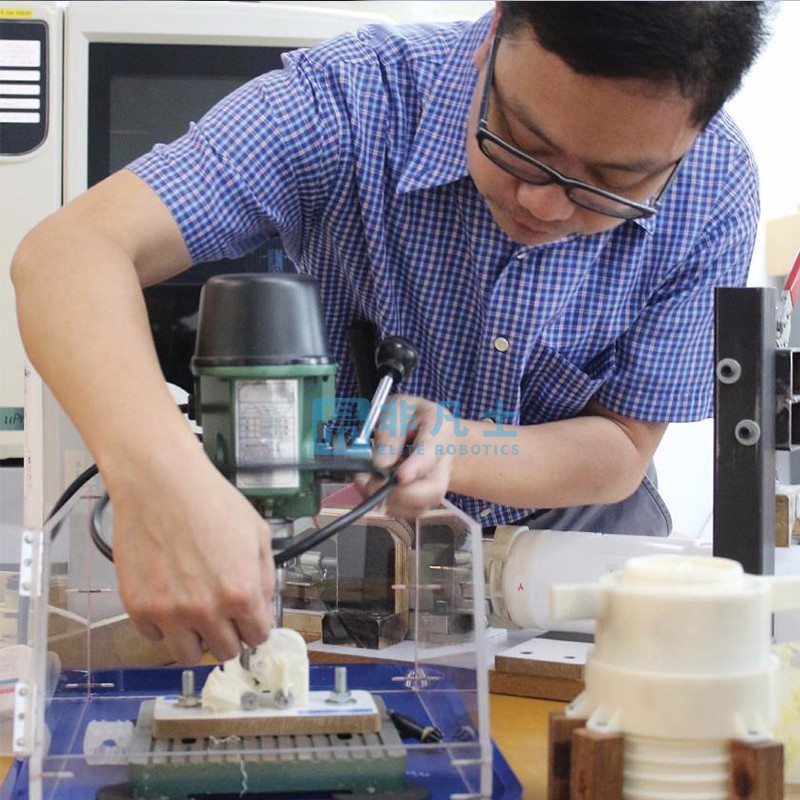
3D 打印还增强了 EC-Atech 的创造力。通过使用FDM 技术,该团队成功设计出了一种工具,该工具可以帮助加快墨盒上胶速度,从而最大程度地减少了人为错误的可能性,并能够确保产品质量始终如一。
|